SPATZ - Pick&Place screwdriving robot with automatic tool change and feed unit for fasteners.
Marca
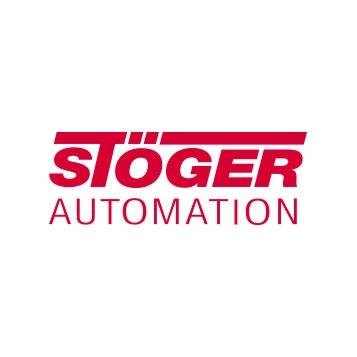
The SPATZ (STÖGER Pick&Place screwdriving robot with automatic tool change and feed unit for fasteners) has all the features to revolutionize the system layout in automated production and offers high savings potential in the design of assembly and manufacturing systems.
The customer's wish to screw several screws together with one system was previously only feasible with high development costs due to technical obstacles and was therefore associated with high costs. This results from the different screw geometries, which require different mouthpieces or feed hose diameters. Due to their geometry, some elements cannot be fed via a tube.
STÖGER AUTOMATION has developed a solution for this requirement and thought one step further.
The SPATZ (STÖGER Pick&Place Screwdriving Robot with automatic tool change and feed system for fasteners) is a modular screwdriving automat that can automatically switch between several screwdriving tools. This is made possible by operation on a lightweight robot, which can teach all sequence positions with a newly developed, intuitive operator software. This means that, in addition to screwdriving, other tasks such as placing workpieces, setting boards, pins, balls, gripping components ... are also possible. There are hardly any limits to the planning of the plant design.
The SPATZ consists of a drive, the tool holder with quick lock, the required screwdriving tools and the corresponding number of feed units. In the standard version, the SPATZ can handle up to 15 different screwdriving programmes. Due to the modular design, all conceivable screw sequences with different screw geometries and screw positions can be mapped and combined with each other.
The modular and flexible design opens up completely new and significantly more cost-effective concepts than before. Since only additional tools are required for different screw geometries instead of additional screwdriving units, the system price is significantly reduced.
The more different fasteners are processed with the SPATZ, the higher the savings potential.
In addition to screwing, many other activities are possible. For example, grippers can also be integrated. Thus one robot can pick up a component, screw in different screws, set balls or pins, assemble components and much more. This opens up completely new possibilities for the system layout.
Software has been developed for the UR robots UR3e, UR5e, UR10e and UR16e of the e-Series, which enables users to store the associated screwdriving programmes and to determine in just a few steps all the positions that the robot has to move to. Extensions and changes to the system layout are also conveniently adapted via an intuitive user interface.